Pre-Cast Shapes
Our precast refractory shapes are engineered for exceptional durability and thermal efficiency, delivering reliable performance in the harshest environments. Manufactured to exacting standards at our UK facility, each shape is designed to meet the unique requirements of your operation—whether for rapid installation, extended service life, or complex geometries.
From standard blocks and burner tiles to bespoke components, our precast shapes are trusted across steel, foundry, incineration, and petrochemical sectors. With a dedicated technical team and rigorous quality control, we ensure every piece is delivered on time and ready for immediate installation. Partner with Robert Lickley for precast solutions that minimise downtime, maximise efficiency, and withstand the demands of modern industry.
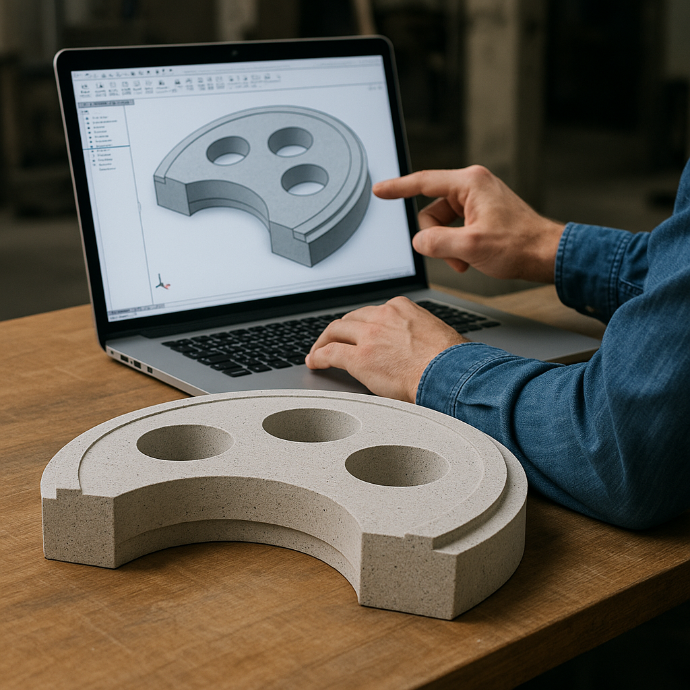
We Design
Our experienced engineering team collaborates closely with customers to design precast refractory shapes tailored to exact process requirements. Using advanced 2D / 3D modelling and years of industry know-how, we turn complex concepts into practical, robust solutions—ensuring every project meets performance expectations, optimises installation, and delivers lasting value in demanding environments.
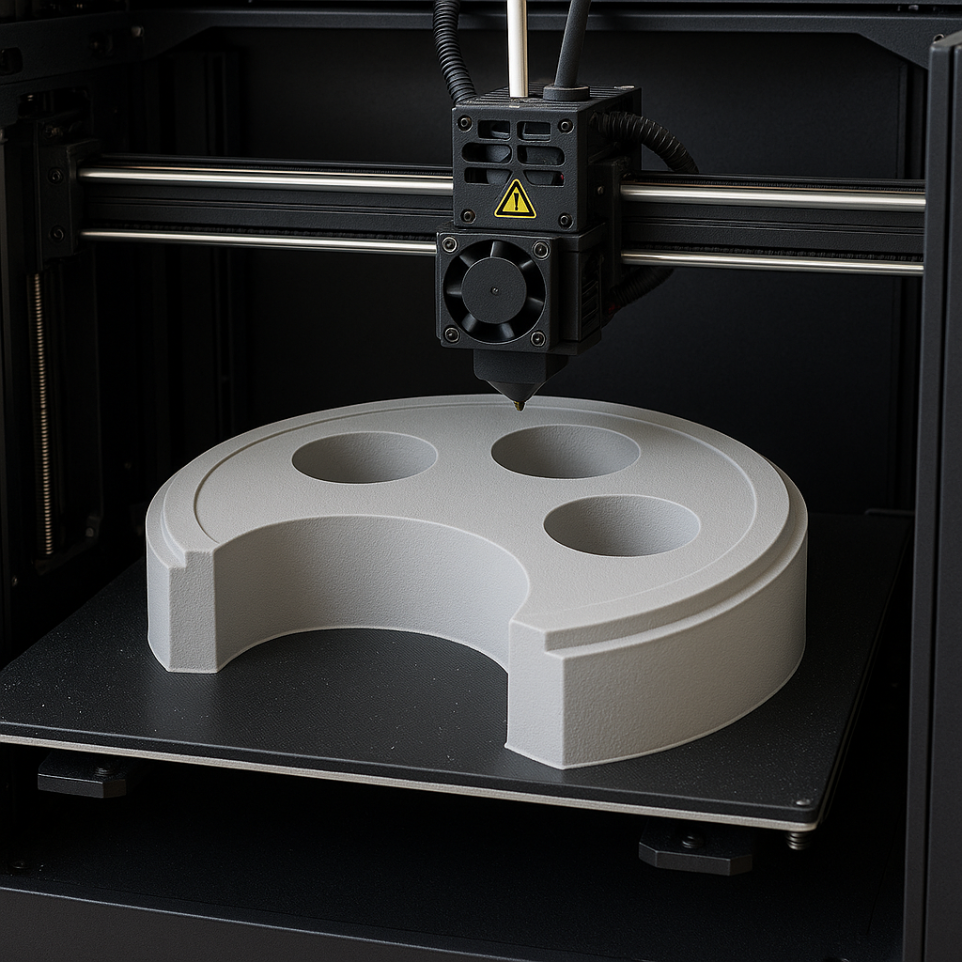
We Prototype
Innovation is at the heart of our service. Using advanced 3D printing and rapid prototyping, we can create accurate models and prototypes of complex refractory shapes before full-scale production. This approach allows for quick design validation, cost-effective development, and ensures you get the perfect fit—saving time, reducing risk, and optimising performance.
We Manufacture
Our skilled production team manufactures each shape at our Dudley facility, combining proven craftsmanship with the latest casting technology. We work with a wide range of high-performance materials to deliver consistently precise and reliable precast components, whether you need standard sizes or fully bespoke solutions engineered to withstand even the harshest operating conditions.
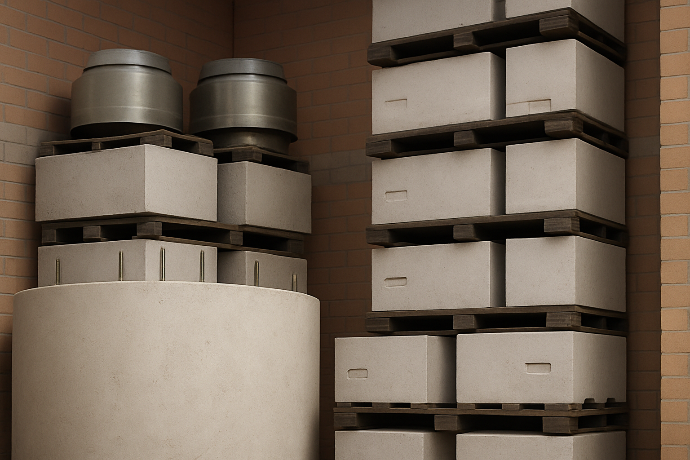
We Dry
Every precast shape is carefully dried in controlled conditions to eliminate residual moisture and minimise the risk of cracking or spalling during commissioning. Our state-of-the-art drying processes ensure products are fully cured and ready for immediate installation, providing peace of mind and helping you avoid unnecessary delays or costly on-site issues.
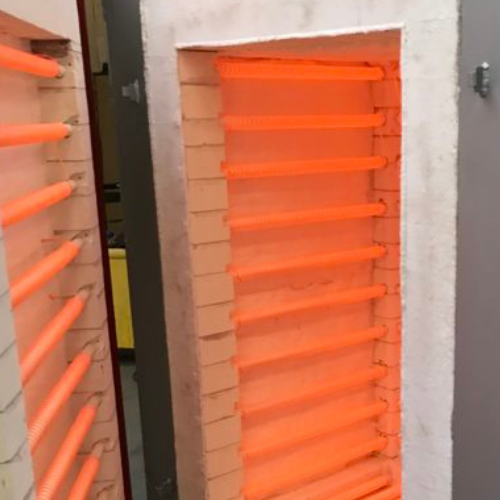
We Fire
Where required, we offer kiln firing to further enhance the strength and stability of our precast shapes. This vital finishing step guarantees thermal shock resistance and long-term durability, making our fired products ideal for the most extreme service conditions. Trust Robert Lickley to deliver fired refractory solutions that stand the test of time.
Our Route to Net Zero
Our environmental commitment is simple.
Net Zero Scope 1 & 2 by the end of 2025.
We have already made huge strides towards this goal through the purchasing of Net Zero electricity and our Carbon offsetting of drying oven fuels.
Our conversion to electric vehicles now stands at 50%.
We have accurately measured our Scope 1 & 2 Emissions and will completely offset anything beyond our control for the whole of 2025.